Innovationsprojekt „Predictive Maintenance“
Neue Wege der Instandhaltung für die Lebensmittelproduktion
Die Herausforderung
Instandhaltung gewährleistet die Funktionsfähigkeit aller Maschinen einer Produktion. Dabei gibt es zwei wesentliche Aktivitäten: Akutes Reagieren auf Störfälle und planbare Regeltätigkeiten, wie zum Beispiel das prophylaktische Austauschen von Bauteilen. Für letzteres sind berüchtigte „Wartungsfenster“ notwendig, im schlimmsten Fall mit Unterbrechung der Produktion. Dabei ist schnell ein Spagat klar: Je prophylaktischer potenzielle Störfallquellen ausgetauscht werden, desto weniger Störfälle gibt es. Aber desto höher sind aber auch die Kosten durch frühzeitigen Materialaustausch und höhere Frequenz an Wartungsfenstern.
Das Ziel des Innovationsprojekts
Ziel des Projektes mit MAXIMAGO war es, die Planbarkeit der Instandhaltung zu maximieren, dabei aber die Zeitpunkte vor einem Störfall bestmöglich abzupassen und damit Intervalle von Wartungsfenstern zu vergrößern.
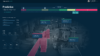
Die Ausgangslage
Das exemplarische Werk war umfangreich mit Sensorik ausgestattet. Die resultierenden Daten wurden zum Zeitpunkt des Projekts bereits zu Auswertungen inklusive Vorhersagen genutzt, was allerdings zu keiner signifikanten Verbesserung der Instandhaltung geführt hat.
Das Vorgehen
Wir setzten zur Product Discovery eine Mischung aus den Methoden „Google Design Sprint“ und Aspekte aus „Design Thinking“ ein.
Ein Kreativ-Workshop leitete die Findungsphase ein. Teilnehmer waren Repräsentanten jeder betroffenen Fachkompetenz. Anschließend wurden die Ideen und Thesen an Teilnehmer zur Verifikation delegiert.
Insgesamt fanden bis zum Konsens zum zu lösenden Problem 4 Iterationen an Workshops und Verifikation statt.
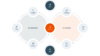
Die Hypothese
Die bestehenden Daten aus der Sensorik und den Vorhersage-Algorithmen waren ausreichend vorhanden – aber nicht den Beteiligten in geeigneter Form zugänglich. Die Instandhaltung ist darauf angewiesen, „Reports“ von der IT anfertigen zu lassen. Das Ergebnis sind viele Zahlen, die schwer im Kontext von Wahrscheinlichkeiten interpretierbar sind.
Die sich im Projektverlauf bestätigte Hypothese: Es braucht eine intuitive Aufbereitung der Daten, die eine Interpretation der Risiken zwar ermöglicht, nicht aber binär vorgibt.
Der Lösungsansatz
MAXIMAGO entwarf einen interaktiven Prototypen, der die Daten aus der Produktion inklusive Vorhersage leicht verständlich aufbereitete. Er wurde so konzipiert, dass er in der Produktionsumgebung auf bereits vorhandenen und den Nutzern bekannten Touch-Devices erlebbar und verifizierbar war.
Verifikation
An Hand von echten historischen Störfällen wurden Ansichten gestaltet, die die tatsächliche damalige Datengrundlage und das Systemverhalten repräsentierte. Nun wurden echte Nutzer nach der Interpretation befragt. Die geplanten Schwellwerte zur optimierten Erkennung und besseren zeitlichen Einstufung waren eindeutige Verifikation des Lösungsansatzes.
Haben wir Ihre Interesse geweckt?
Weiterführende Informationen zum Portfolio-Bestandteil „Innovationsprojekte“ finden Sie hier: Innovationsprojekte
Gerne stehen wir Ihnen aber auch persönlich direkt zur Verfügung: